MIP, COB and SMD are three prominent options within LED display packaging technology. LED display packaging technology can currently be broken down into three distinct phases:
- traditional LED packaging;
- Mini-LED packaging
- Micro-LED packaging.
There are Three Mini-LED packaging technologies:
- SMD
- COB
- IMD.
SMD LED packaging can cover applications with pitches of P0.9 or greater. While COB LED technology offers slightly greater reliability for smaller LED screen applications but may be susceptible to damage when applied directly on surfaces such as LED film displays.
COB LED technology eliminates the SMT component, making it suitable for pitch ranges from P0.4 to P2. This technology can provider uniform surface illumination. However, it can have problems with color consistency.
IMD combines the benefits of both SMD and COB technology, offering pitch ranges of P0.4 to P0.9 with strong resistance to damage and enhanced reliability.
Micro-LED packaging involves several techniques, such as single-chip integration, micro-array lens optical synthesis, UV/B Micro-LED arrays with RGB quantum dot color conversion capability and full color RGB Micro-LED-based MiP packaging.
What Is Micro LED Packaging Technology?
MiP, or Micro LED in Package, is an exciting technology that combines micro LED chips with high precision substrates to facilitate fan-out packaging. MiP also allows for full testing, sorting and bundling of RGB Micro pixels ensuring high display uniformity as well as streamlining manufacturing costs making mass production feasible.
MIP technology optimizes Micro-LED packaging by breaking large LED display panels down into smaller sections, significantly improving yield control and lowering costs. Furthermore, testing is moved from chip production to packaging stage to further lower cost while making better use of existing equipment.
MIP LED modules increase benefits in terms of product performance such as higher black levels, special optical designs, strong compatibility and diverse applications. MIP packaging makes post-production testing and repairs simpler as well.
Advantages of MiP LED display
Here are the Advantages of MiP LED display Like Below:
Advantage | Description |
---|---|
Better displaying effect | Extremely high brightness, contrast, and color consistency from different viewing angles due to full measurement of Micro RGB pixel, color sorting, and mixing. |
Much less maintenance | Based on MCOB module, MiP mounting has consistent ink color and needs no correction, requiring much less maintenance due to its impeccable light splitting and color mixing features. |
Easy replacement | Faulty lamps can be easily removed and replaced without affecting the rest of the screen, thanks to MiP technology. |
Wide compatibility | Mass production; it can reduce wafer costs compared to traditional COB technology which has stricter requirements for mini LED chips. |
Much lower cost | It can reduce costs by being compatible with existing equipment, decreasing defective screening rate, and reducing downstream rework costs. |
Good protection | Offers perfect protection of LED lamps from dust, moisture, and static electricity through MiP packaging technology. |
Better heat dissipation | MiP LED modules have improved heat dissipation, leading to less LED screen power consumption and temperature rise. |
What Is COB LED Packaging Technology?
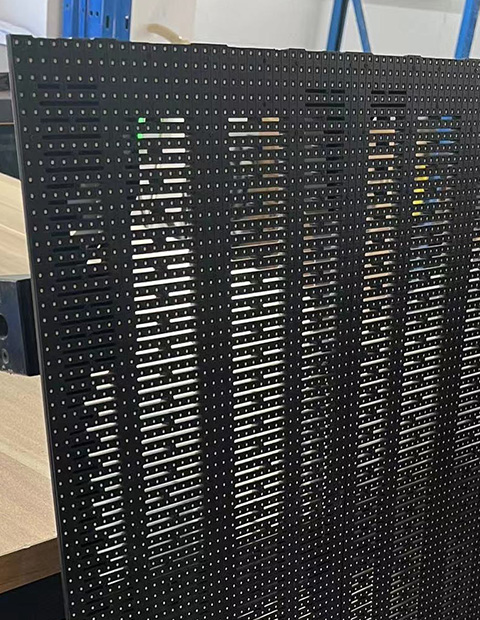
COB, or Chip-on-Board packaging, differs significantly from surface mount (SMD) packaging in its application of adhesive bonds to attach LED chips directly onto PCBs using either conductive or non-conductive glue, bonding wire connections to them, and encapsulating chips and bonding wires together using glue. COB LED technology integration simplifies manufacturing by consolidating LED display module production within one factory, increasing reliability and simultaneously decreasing costs.
At present, COB packaging technology is moving in three key directions.
Single-Chip COB Packaging:
Similar to traditional methods of LED packaging, with lower technical barriers. LED Display manufacturers purchase pre-packaged COB LED chips from suppliers and install them one by one onto LED display panels using SMT technology.
Limited Integration COB Packaging:
Some LED display manufacturers are turning to limited integration COB LED packaging to improve production efficiency, decrease pixel failure rates and bypass complex packaging processes. LED Display manufacturers purchase COB LED modules from packaging facilities before using SMT technology to attach these modules directly onto LED display panels.
COB Integration Packaging:
COB integration packaging provides very high integration levels, typically exceeding 0.5k and even exceeding 2k integration levels in some cases. COB LED packaging allows full LED chip integration during packaging phase thereby eliminating SMT processes altogether and saving time and costs compared to traditional SMD LED processes. Its often referred to as “non-packaging” or “reduced packaging”, as certain steps of the packaging process can be skipped for greater efficiency compared to traditional SMD methods.
Several challenges to COB LED packaging in the LED display industry.
First Pass Yield in Packaging Process:
COB LED packaging involves attaching multiple LEDs (up to 1024 on one board). Unlike SMD LED packaging, where individual faulty LEDs can be replaced individually, COB requires thorough testing of all 1024 LEDs before encapsulation – and assuring that all 1024 are functional on their initial attempt is a major challenge.
First Pass Yield of Finished Products:
Following LED encapsulation, COB products undergo reflow soldering to connect their IC driver components. Reflow soldering at high temperatures (240 degrees) must avoid damaging LEDs during this process and protect their surfaces during reflow to maintain product integrity; COB faces this challenge by eliminating surface reflow, yet still must undergo it with its IC components; unlike SMD which faces two potential sources of damage during reflow; high temperatures must not harm COB products’ quality, thus guaranteeing product quality during reflow soldering process.
Whole-Unit Maintenance of COB LEDs:
Maintaining COB LEDs requires expert knowledge as individual repairs may cause visible ring of heat distortion around them and make repairs even more complicated.
To meet these challenges, industry has devised solutions. Protective measures during reflow soldering may help reduce LED damage while point-by-point calibration techniques may ensure consistency among LED chips.
COB LED packaging has the advantage of being directly integrated with PCB boards, providing flexibility with regards to pixel pitch. COB is often used for high density applications; according to an industry professional, its use may even make sense in smaller-pixel pitch LED display market.
At present, many LED display manufacturers are following dual development paths of SMD and COB. P1.0 or smaller LED displays are typically produced using both IMD and COB technologies; both technologies can accommodate specifications ranging from P0.4 to P0.9. MIP can also be considered an independent pixel-level COB packaging method, offering reliability along with individual LED flexibility; it remains particularly advantageous when applied to larger applications like P1.2, P1.5 and even P3.0 applications; MIP’s versatility means it works for different pixel pitches as well as mixed binning options that deliver superior performance on larger displays.
COB technology excels in high-density, integrated packaging. It is generally found in mid to high-end segments and typically used for up to P1.6; P1.2 being most prevalent. As the pixel pitch decreases, its comprehensive cost advantage becomes clearer; when P1.2 or less pixels are present COB’s manufacturing costs become lower than SMD technologies.
Differences between COB packaging and MIP packaging:
Different principle:
COB LED displays offer higher quality due to eschewing brackets for direct chip placement on substrate, using either silicone or conductive glue directly and wire bonding for electrical connection; in comparison, MIP packaging involves interconnecting LED chip electrodes with substrate electrodes through an interconnection rack once their production has begun.
Different characteristics:
COB LED packaging has the advantages of beautiful appearance, simple structure, and low cost. MIP packaging has the advantages of ultra-thin packaging, high production efficiency, and good heat dissipation performance. COB LED technology integrates the midstream packaging and downstream display technology of the LED industry, eliminating the cost of brackets and part of the manufacturing process, resulting in higher production efficiency;
The MIP technology can better realize the cost reduction and quality improvement of Micro LED. The comprehensive manufacturing cost of MIP technology is lower than COB technology and SMD technology.
Technology | Advantages | Disadvantages |
---|---|---|
SMD | Most mature LED package technology. | – Lower reliability due to potential damage or failures during production. – Difficulty achieving pixel pitches below P1.0 due to physical size. |
COB | Can reach small pitches suitable for mini-LED and micro-LED. | – Maintenance is challenging; difficult to repair a single lamp. – Welding can damage surrounding lamps. |
IMD | Combines advantages of SMD and COB; covers small pixel pitches (0.4 – 0.9mm); better anti-bumping feature. | – Limited to specific pixel pitc |
Related Article:
What are GOB LED Display vs. COB LED Display?
Conclusion:
COB LED packaging increase numerous advantages, such as high quality, cost effectiveness and space efficiency, but does pose some unique testing and reflow soldering challenges that need to be met in a cost-effective manner. These obstacles have been met through industry innovation solution ; COB LED technology being ideal for higher density applications while MIP stands out as being especially good at supporting larger pixel pitch LED displays.