In recent years, as LED display technology has accelerated its evolution towards micro-pitch (below P1.0) and Micro LED fields. COB packaging technology has high stability, high protection and excellent display effects,which has gradually become the mainstream of the industry. However, do you know the difference between “Wire Bond and Flip chip COB”? . GDHANHENG will deeply analyze COB technology and explore the technical advantages and future trends of full Flip chip COB.
What is COB technology?
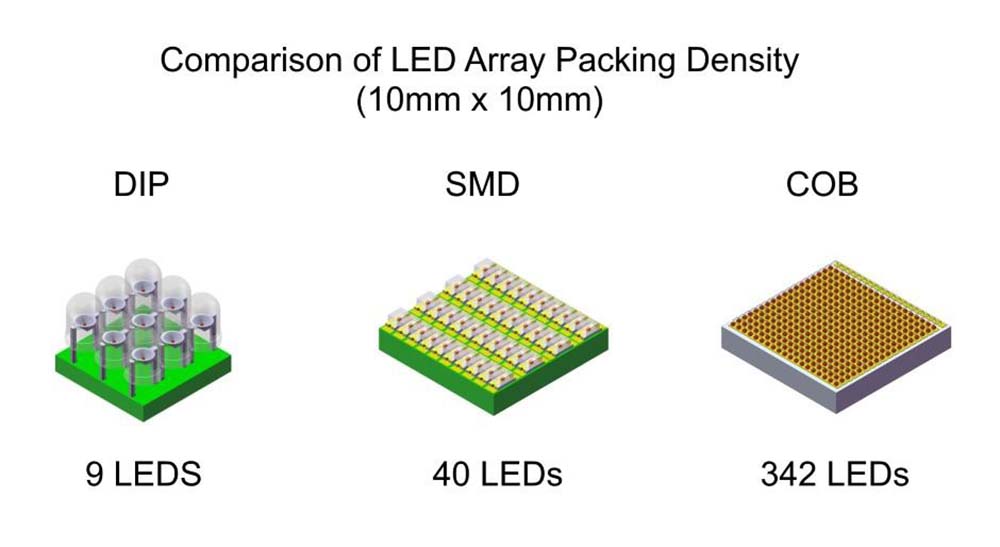
COB is chip-on-board packaging technology. Its core is to directly bond LED chips to the PCB board for integrated packaging. Compared with traditional SMD technology, which requires the chip to be packaged into lamp beads before patching, COB eliminates the intermediate links and has three breakthrough advantages:
SMD technology:
- The RGB three-color LED chip must be packaged into lamp beads first;
- Then the lamp beads are soldered to the PCB board through the SMT patch process to form a display module.
COB technology:
- Directly bond the LED chip to the PCB board
- Then perform integrated packaging
- Eliminating the lamp bead packaging process.
Advantages of COB Packaging:
Higher production efficiency: Reduce packaging steps and improve manufacturing efficiency.
Better imaging quality: Smaller chip spacing, higher pixel density, and more delicate pictures.
Stronger protection: The packaging layer directly covers the chip, and the moisture-proof, dust-proof, and collision-resistant performance are significantly improved.
Micro-pitch adaptability: It is suitable for ultra-small pitch scenes below P0.6, meeting high-end display requirements.
What is a regular Wire Bond COB LED Packaging?
Definition: All three RGB chips are packaged on the PCB board using regular Wire Bond LED chips.
Advantages:
- Low cost: Regular chip technology is mature and the price is much lower than flip chip.
Defects:
- Unstable wire bonding process: Regular chips need to connect electrodes to PCB boards through gold wires. Metal migration is prone to occur in humid environments, resulting in problems such as dead lights and caterpillars, and reduced product yield.
- Limited light output efficiency: The front electrode blocks the light-emitting surface, and the light efficiency loss is significant.
- Poor heat dissipation performance: The contact area between the electrode and the PCB is small, and heat accumulation affects the lifespan.
- Obvious technical ceiling: In the field of Micro LED (below P0.6), the upright COB has lost its competitiveness due to the limitations of chip size and spacing.
What is mixed COB Packaging?
Definition: RGB chips are packaged in a mixed manner of Wire Bond and flip-chip, such as “two flip-chips and one Wire Bond” (2 flip-chip blue-green chips + 1 Wire Bond red chip).
Background of birth:
Around 2020, the price of flip-chip red chips was high, and the mixed solution reduced costs through “upright red light + flip-chip blue-green”.
Current situation:
As the cost of flip-chip red chips decreases, the mixed solution is gradually eliminated by the market due to its dual disadvantages in performance and cost.
What is full flip-chip COB packaging?
Definition: All three RGB chips are packaged on the PCB board using flip-chips.
Core advantages:
- No solder wire design: The electrode is directly bonded to the PCB board, completely eliminating the risk of solder wire failure, and extending the module life by more than 50%.
- High stability: The solder pin spacing is larger, the probability of electron migration is reduced, and the dead light rate is close to zero.
- Efficient luminescence: There is no electrode blocking the front of the chip, the luminous area is increased by 20%, and the luminous efficiency and contrast are significantly better than the regular COB.
- Micro-pitch adaptation: Supports ultra-small pitch below P0.4, the only technical path to achieve mass production of Micro LED.
The core difference between regular and flip-chip COB
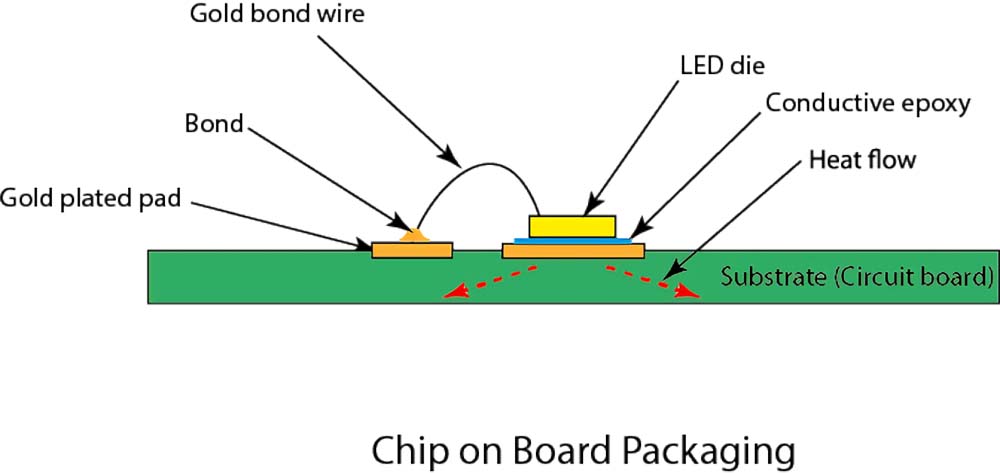
Packaging structure:
Regular: The chip faces up, and gold wire is required to connect the electrode.
Flip-chip: The chip is inverted, and the electrode is directly bonded to the PCB.
Stability:
Regular: The welding wire is easy to fall off and easy to fail in a humid environment.
Flip-chip: No welding wire, more solid bonding, longer life.
Luminous efficiency and contrast:
Regular: The electrode blocks the luminous surface, and the luminous efficiency loss is about 15%.
Flip-chip: The luminous area is larger and the contrast is increased by more than 30%.
Cost and process:
Regular: Low cost, simple process, but low technical ceiling.
Flip-chip: high cost, but significant performance advantages, adaptable to future micro-pitch needs.
Application scenarios:
Regular: It is suitable for conventional pitches above P1.0, cost-sensitive projects.
Flip-chip: covers the full pitch of P0.4-P1.8, the first choice for high-end display and Micro LED.
What are the advantages of IAMLEDWAll’s full flip-chip Mini COB LED display?
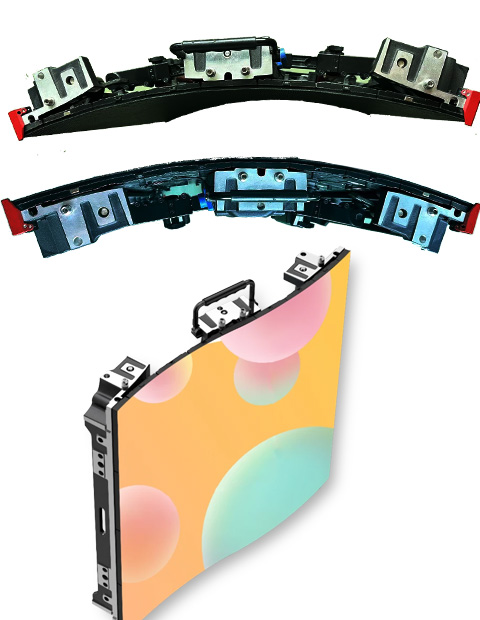
With independent research and development capabilities, GDHANHENG has successfully realized full flip-chip COB packaging technology.
Our full flip-chip MiniCOB core advantages
Higher reliability:
No solder wire packaging, eradicating failure risks
Common COB pain points: Traditional formal COB relies on gold wire to connect electrodes and PCB boards, which is prone to metal migration in humid environments, resulting in wire breakage, dead lights or “caterpillar” phenomena, and product yields less than 80%.
Our flip-chip solution:
Electrode direct connection technology: The flip chip is directly bonded to the PCB board through solder joints, completely eliminating solder wires, and reducing the risk of failure by more than 90%.
Anti-metal migration design: The solder pin spacing is expanded to 2 times that of the regular chip, the probability of electron migration is close to zero, and the module life exceeds 100,000 hours.
Severe environment verification: Passed -40℃~85℃ high and low temperature cycle test and 85%RH humidity impact test to ensure stable operation of the product in extreme environments.
Higher contrast:
Regular COB limitations: The front electrode blocks the light-emitting surface, the light efficiency loss is about 15%, and the contrast is limited.
Our flip chip innovation:
Electrode-free shielding design: The flip chip electrode is located on the back, the light-emitting area is increased by 20%, and the light efficiency is 1.3 times that of the regular COB.
Micro-pitch adaptability: The P0.4 chip size is reduced to less than 50μm, combined with high-transmittance packaging glue, to achieve an ultra-high contrast ratio of 15000:1, no light leakage in dark field pictures, and no halo in bright field pictures.
Energy saving and efficiency improvement: At the same brightness, power consumption is reduced by 30%, which helps green display.
More excellent picture quality:
Our full flip-chip Mini COB series products use “2000nits high brightness, 15000:1 high contrast, 7680Hz high refresh rate, 120% NTSC ultra-wide color gamut” as core indicators to redefine high-end display standards:
2000nits high brightness: adapted to outdoor light environment, ensuring clear images under strong light.
7680Hz ultra-high refresh rate: eliminates dynamic blur and meets the needs of high-speed sports scenes such as sports events and virtual shooting.
120% NTSC ultra-wide color gamut: covers 90% of the DCI-P3 color gamut, with color reproduction of ΔE<1, achieving movie-level picture quality.
HDR dynamic optimization: supports HDR formats such as HLG and Dolby Vision, with no overexposure in bright areas and details in dark areas.
Full-pitch coverage capability:
We have achieved full-pitch mass production of P0.4-P1.8 through the dual-wheel drive of “chip miniaturization + packaging process upgrade”:
P0.4-P0.7 ultra-small pitch: using Micro LED chips below 50μm, adapted to scenes with extremely high pixel density requirements such as high-end conference rooms and command and control centers.
P0.8-P1.2 small pitch: balancing cost and performance, widely used in commercial complexes, exhibitions and other fields.
P1.2-P1.8 conventional pitch: meeting the display needs of education, medical and other industries with high cost performance.
Customized solution:
High refresh rate mode: supports 120Hz/240Hz/7680Hz multi-speed switching, adapted to different content sources.
High brightness mode: peak brightness can be increased to 3000nits, meeting outdoor or semi-outdoor scenes.
Large module design: Single module size covers 600mm×337.5mm to 1600mm×900mm, reducing the splicing gap and improving visual integrity.
Technical moat:
Our full flip-chip Mini COB technology leadership stems from the full industry chain integration capabilities of “chip design-packaging process-equipment development”:
Chip end: Jointly develop flip-chip Micro LED chips with upstream manufacturers to optimize electrode layout and luminous efficiency.
Packaging end: Independently develop high-precision die bonding equipment and packaging glue to achieve chip spacing error <±1μm and packaging yield >99%.
Equipment end: Break through the bottleneck of mass transfer technology, increase the production capacity of a single device to 10KK/month, and reduce mass production costs.
Continuous innovation:
Third-generation packaging technology: Develop “chip-level optical bonding” process to further reduce optical path loss, and mass production is expected in 2025.
Intelligent operation and maintenance system: Integrated AI fault diagnosis module, real-time monitoring of module status, predictive maintenance to reduce downtime risks.
Market value:
The commercialization of our full flip-chip MiniCOB is reshaping the industry landscape:
High-end market replacement: Replace traditional SMD small-pitch products with performance advantages to seize the high-end commercial display market.
Micro LED popularization: Promote Micro LED from “concept” to “mass production” through technology cost reduction, and accelerate penetration into the consumer market.
Eco-synergy: Build a Micro LED industry alliance with upstream and downstream companies to promote standard formulation and ecological improvement.
Typical application scenarios:
Smart control center: 7680Hz refresh rate + 15000:1 contrast ratio to ensure that massive data is visible in real time without smearing.
Virtual shooting studio: 2000nits brightness + 120% NTSC color gamut to meet the needs of movie-level picture capture.
High-end retail space: Ultra-narrow frame large module design to create an immersive shopping experience.
How much does a COB LED screen cost?
The price of a COB LED screen is affected by multiple factors such as packaging technology type and dot pitch. The following is a comparison:
Pixel Pitch (mm) | Conventional COB (10,000 yuan/㎡) | Full Flip-Chip COB (10,000 yuan/㎡) | Price Difference Analysis |
---|---|---|---|
P1.2 | 3-5 | 6-8 | Full flip-chip COB is 50%-100% more expensive due to higher chip costs and complex packaging processes compared to conventional COB. |
P0.9 | 5-7 | 8-12 | At ultra-fine pitches, the yield rate of conventional COB decreases, while the performance advantages of full flip-chip COB become more prominent, further widening the price gap. |
P0.6 | -(Technical bottleneck) | 15-20 | Conventional COB cannot be mass-produced due to wire bonding failures and insufficient luminous efficiency. Full flip-chip COB becomes the only viable option, reaching the industry’s price ceiling. |
Notes:
The price range is based on the quotations of mainstream brands in the market in 2024. The actual transaction price fluctuates by 10%-20% due to brand, purchase volume, and customization requirements.
In the Micro LED field below P0.6, the price of full flip-chip COB is limited by chip production capacity in the short term, but will gradually decrease as the technology matures.
Full flip-chip COB long-term cost model: 10-year comprehensive cost comparison
Take the P0.9 pitch and 100㎡ LED display screen as an example:
Cost Item | Conventional COB (10,000 yuan) | Full Flip-Chip COB (10,000 yuan) | Difference Analysis |
---|---|---|---|
Initial Investment | 500-700 | 800-1200 | Full flip-chip COB has 50% higher initial costs. |
10-Year Maintenance Cost | 120-160 | 20-40 | Full flip-chip COB reduces maintenance costs by 80%. |
10-Year Energy Cost | 180-220 | 100-140 | Full flip-chip COB saves 40% on energy consumption. |
Total Cost | 800-1080 | 920-1380 (Initial) → 760-1060 (10-Year) | Full flip-chip COB has 10%-20% lower total cost over 10 years. |
Conclusion:
Although the initial investment of full flip-chip COB is high, the total cost in 10 years exceeds that of regular COB, and the display effect and stability are significantly better.
In high-end commercial display, command and control center and other scenes with extremely high reliability requirements, the long-term value of full flip-chip COB is particularly prominent.
Price trend and procurement recommendations
Technical cost reduction path:
Chip side: Micro LED chip yield is improved, and the cost is reduced by 15%-20% annually.
Packaging side: The localization rate of equipment is increased, and the packaging cost is reduced by 30%.
Prediction: In 2025, the price of P0.9 full flip COB is expected to drop to 60,000-80,000 yuan/㎡, and P0.6 to 100,000-150,000 yuan/㎡.
Procurement strategy:
High-end scenarios: give priority to full flip COB to ensure long-term stability and low maintenance costs.
Cost-sensitive scenarios: For P1.2 and above, you can choose regular COB, but you need to reserve 20% of the budget for later maintenance.
Long-term planning: Consider the 5-10 year technology upgrade cycle to avoid frequent replacement due to short-term low-price solutions.
Conclusion:
As technology matures and costs fall, full flip COB LED display will become the standard in the high-end display market. They will promote the upgrade of LED display from “price competition” to “value competition”. If you need COB LED screen, please feel free to contact us.